Photo Credit: Eugenia Uhl
Intralox Hammond is a plastics manufacturing plant, distribution warehouse and office space. This 400,000 sq. ft. new construction structure incorporates 19,200 cubic yards of concrete and 2,700 tons of structural steel. This expansion ties in directly to the preexisting manufacturing facility, tripling operations.
Intralox Hammond is a custom and intricate mega-project accommodating Intralox L.L.C.’s specialized manufacturing processes and global distribution. The Owner’s goal for this project was to expand the existing Intralox Hammond facility to support increased production and assembly operations of modular plastic conveyor belts used in food, industrial and ecommerce industries across the world. The identified requirements included maintaining operations of the existing facility and an extremely fast-tracked delivery.
Design-Build Enhanced Processes and Innovations
The design-build model allowed for simultaneous design documentation development and preconstruction value engineering efforts. This early identification of cost-saving opportunities then facilitated Early Subcontractor Involvement. Trade partners adopted a design-assist role, offering specialized knowledge on critical scopes of work to guide the project’s development.
The design-build nature of the project allowed for cross-discipline innovation, ultimately achieving Owner Project Requirements and goals, including that 15% of the warehouse space be fully functional to support operations within 10 months. Team alignment on expectations during project kick-off was critical in exceeding lifecycle cost and addressing long-term project performance goals.
The streamlined approach fundamental to the design-build team model was critical in managing the scope amidst a volatile, unprecedented market. Material procurement issues threatened the project’s fast-track delivery; many critical scopes skyrocketed in price, doubled or tripled in lead time, or became unavailable altogether. The team employed VDC technology to explore alternative design solutions. The initial bar-joist roof system threatened the project’s fast-track delivery, as the bar-joists themselves were unavailable. The design team used the BIM Model to assess alternative options, considering overall constructability and potential impact to other scopes. Ultimately, the team quickly pivoted to the use of W sections in lieu of bar joists and altered the building’s design accordingly. The BIM Model was critical in maintaining comprehensive quality control in developing the best solution.
Design-Build Team
Client/Owner: | Intralox, L.L.C. |
Design-Build Firm: | Broadmoor, LLC |
Architect: | Broadmoor, LLC |
Engineers: | Morphy Makofsky, Inc.; GVA Engineering, Fox-Nesbit |
Specialty Contractors: | Gallo Mechanical, LLC; Hi-Tech Electric; Merit Sprinkler |
Owner Advisor: | Intralox, LLC |
Project Cost: | $82.3 Million |
Construction Duration: | 22 Months |
Photos
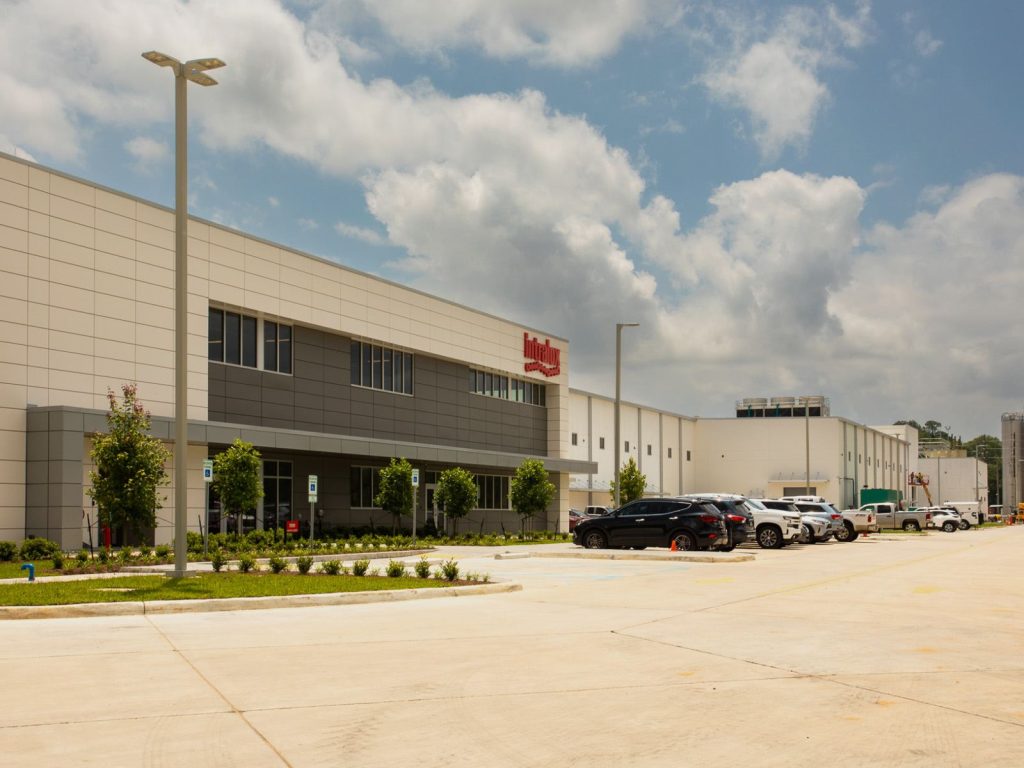

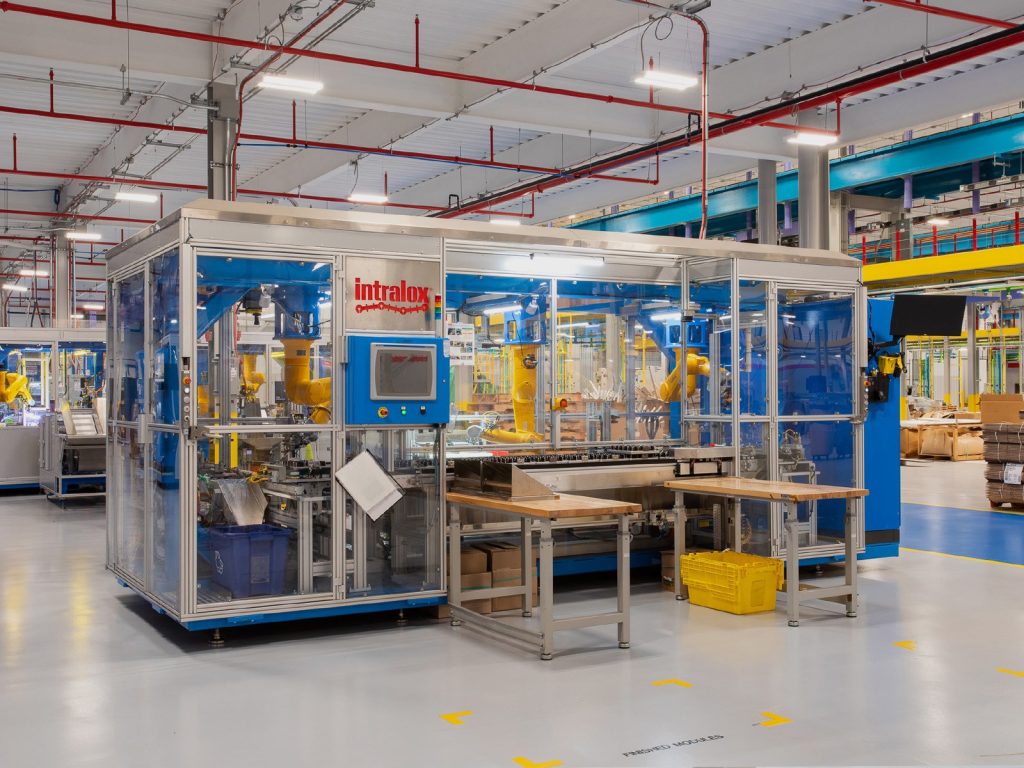