Additional Resources
Once considered “an alternative form of project delivery,” design-build is now the fastest growing and most commonly used project delivery method in the United States. FMI projects design-build to represent over 47% of spending by 2026 and account for $1.9 trillion in construction spending nationwide over the next five years. It is widely used for both private and public sector (federal, state and municipal) projects and across all project types, including vertical (building) construction, transportation and water/wastewater markets.
In all other project delivery methods, there are separate contracts for design and construction. The single contract for both design and construction is the fundamental difference between design-build and other project delivery systems.
But design-build is more than a sole-source contract. It is as much a mindset as it is a process. It is intended to be a highly collaborative, fully integrated undertaking that is built on trust, mutual respect, teamwork, innovation and creative problem solving. Design-build works best when everybody makes the mental shift to think and act as a single entity focused on achieving shared project goals.
DBIA’s Universal Design-Build Best Practices is a good place to start your design-build journey. This document categorizes 10 best practices and nearly 50 supporting implementing techniques into three areas 1) Procuring Design-Build Services, 2) Contracting for Design-Build Services and 3) Executing the Delivery of Design-Build Projects.
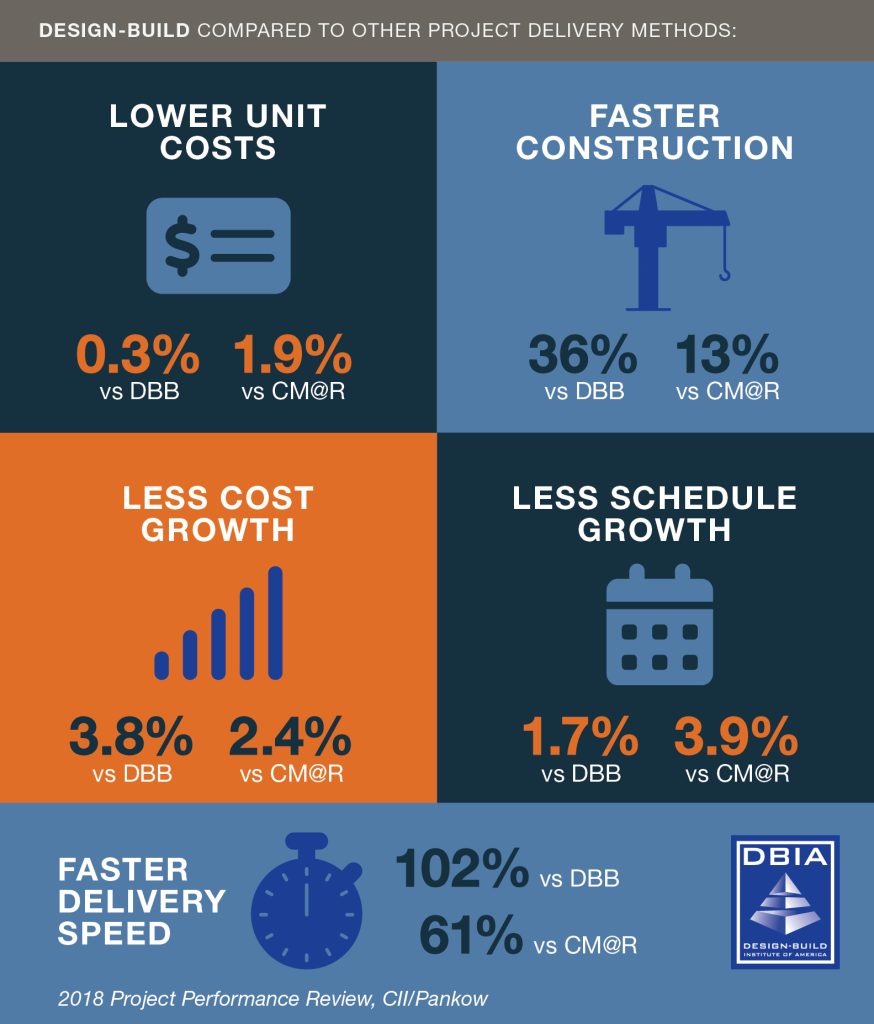
Why Choose Design-Build?
Research over decades has consistently shown the innovation and collaboration inherent in design-build leads to faster project delivery, with more reliable performance and less cost and schedule growth.
Some of design-build’s benefits versus other project delivery methods:
- Higher quality project outcomes
- Collaboration that drives innovation
- Faster, more cost-effective project delivery
- Fewer changes, fewer claims and less litigation
- Allocation of risk to those who can best manage it
- Earlier knowledge of firm costs
With proven benefits like minimized Owner risk, cost savings and accelerated project completion, design-build stands at the forefront of successful and innovative project delivery.
Design-Build Flexibility
The growth of design-build can be attributed in part to the flexibility of Owners to choose a procurement approach or variation best suited to their needs and culture. The most popular variations of design-build are:
- Two-Step Best Value Design-Build
A two-step procurement process first identifies the most highly qualified design-builders then seeks design and cost proposals. The Owner selects the design-builder offering the best value proposal (a combination of design, project approach and contract price).
- Progressive Design-Build
The design-builder is selected primarily on the basis of qualifications. After selection, the Owner and design-builder collaborate to progressively advance the design and cost model toward a mutually agreeable design concept and contract price.
View DBIA’s Position Statement on the Flexibility of Design-Build or the Project Delivery Primer for a deeper dive into these variations.
Resources
DBIA offers a number of additional resources to download in our online Bookstore to help deepen your design-build knowledge:
Primers and Deeper Dives Position Statements Research and Reports Contract DocumentsDebunking Myths
Despite design-build’s impressive growth from what was once considered an alternative project delivery method to one that is now more mainstream, there are still many myths surrounding design-build, and it’s important to dispel them by providing the facts. Read some of the most common myths we often hear.
View Design-Build Myths & Facts Download Myths & Facts One-SheetProjects Database
The DBIA Projects Database is a unique place to browse hundreds of successful design-build projects. The Projects Database is searchable by project type, size and location and provides detailed information about cost/schedule, added value and innovative solutions that resulted from a collaborative design-build approach.
Search Project Database