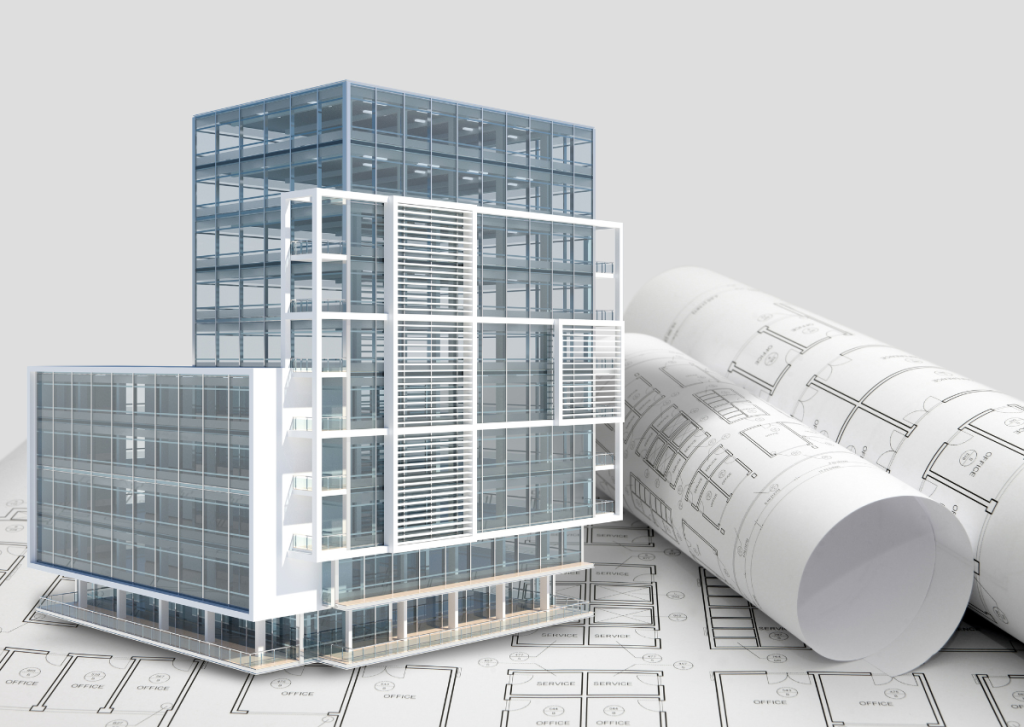
With the abundance of hardware, software, robotics and now artificial intelligence, I often wonder why we’re still doing things the same way in the AEC industry. Projects usually follow the same process: conceive, design, deliver, operate, renovate, demolish, repeat. Even in design-build, which adds consistency by engaging the whole team throughout the process, we aren’t leveraging technology to revolutionize collaboration and transparency as well as we could be.
Design-build teams are similar to teams utilizing other delivery methods. They include Owners, architects, engineers, contractors, consultants and other practitioners dedicated to completing the Owner’s vision for a successful project. Traditionally, team members continuously produce the work required to meet the next deadline or milestone, and at the end of a phase, documents are combined, and the work is evaluated. This leads to requests for information (RFIs), cuts to project scope/cost and change orders, all of which cost valuable time and resources.
Why is this still the case, especially with current technology? With today’s cloud-based technologies, any one member of any team should be able to receive and provide real-time input throughout a project. There is technology available that allows for existing formats, such as UniFormat and MasterFormat, to develop new collaborative and transparent ways to work. Before any drawing is started, anyone involved in the process should review the Owner Project Requirements and start written documentation. Teams can capture the information in UniFormat, and Conspectus has developed a cloud-based tool that allows all project team members to review and verify data prior to beginning drawings.

A Brief History of Classifying Building Specifications
Let’s explore how a structured documentation format can record decisions and build trusted content by briefly examining the history of similar systems for classifying building specifications. In the 1970s, systems developed by the U.S. General Services Administration (GSA) and the American Institute of Architects (AIA) came together to become UniFormat, a systems/assemblies approach to document the building logically, from the bottom up, outside to inside. ASTM International later developed UniFormat II, a standard based on the UniFormat system, and the Construction Specifications Institute (CSI) and Construction Specifications Canada (CSC) revised the system to UniFormat beginning in 1995.
The entire history of these systems is complex, but for this article, let’s focus on the key point: both systems exist and share many similarities. They were developed to unify the common data structures used throughout the lifecycle of the built environment. So, which one should you use? Well, why not both? UniFormat II uses Elements A through G, while UniFormat uses Elements Introduction through Z. Elements A through G are essentially the same for both systems, except for the placement of stair elements. Element D in UniFormat II covers services and MEP (Mechanical, Electrical and Plumbing) work, but it is organized slightly differently in UniFormat. Additionally, CSI/CSC added an Introduction section in UniFormat to cover essential planning and design considerations such as programming, development, budgeting, procurement and contracting requirements. Element Z in UniFormat covers general items typically found in Division 01 of the Project Manual.
Some Guidance on How to Leverage Technology for Design-Build
Let’s further explore how the documentation format records decisions and builds trusted content. UniFormat numbers are represented by an Element Letter, for instance B for Shell, followed by two pairs of numbers, such as 2010, which further defines the assembly. Following that are recommended numbers and letters for estimating, but these can also be customized. If you are familiar with Revit, this is the beginning of assembly codes. A design-build contractor or architect could quickly adapt these UniFormat numbers to align with assembly codes or estimating software.
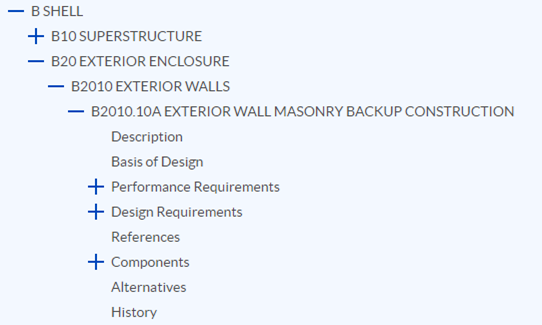
Uniformat can also be used as the construction specifications. Each element in the assembly typically contains the following and is added when the decision is known or made:
- Description: In one concise statement, tell everyone the critical information, what it is and where it is in the building.
- Basis of Design: List them here if one or more are determined.
- Performance Requirements: Describe the salient features to ensure proper building and material performance.
- Design Requirements: Describe any aesthetic requirements essential to the facility’s design.
- References: List any industry standards or references that are crucial to the proper use or implementation of systems.
- Components: Provide a list of all materials required to construct the assembly. This would also directly correlate to the typical 6-digit MasterFormat number in specifications.
- Alternatives: List any alternative ideas currently available to assist with value engineering.
- History: Provide a concise history of when the issues above were resolved, changed, approved or other.
UniFormat numbers are used in estimating and quantity takeoff. By assigning costs to elements earlier in the project, the teams could do actual value engineering by finding the proper systems and materials for the project before the need for cost-cutting. They may also be applied to building operations and maintenance for easy access to information on the materials used to construct the facility. Ordering maintenance and repair parts becomes more straightforward, and if tied to Revit, record documents make it easy to find the locations. The numbers may also be tied to the Level of Development for the Revit model to plan how model elements will evolve by different authors at different stages throughout the project.
With current cloud access, all members of the team can have accurate, up-to-date information available on a mobile device, tablet or laptop computer. Whether you are an Owner establishing an OPR or a superintendent on a job site, you can open up UniFormatUniFormat elements, a full MasterFormat Specification or drawings on a device and get the latest information. Ask a question, inform the team, decide and collaborate transparently –– driving trust and transformation!
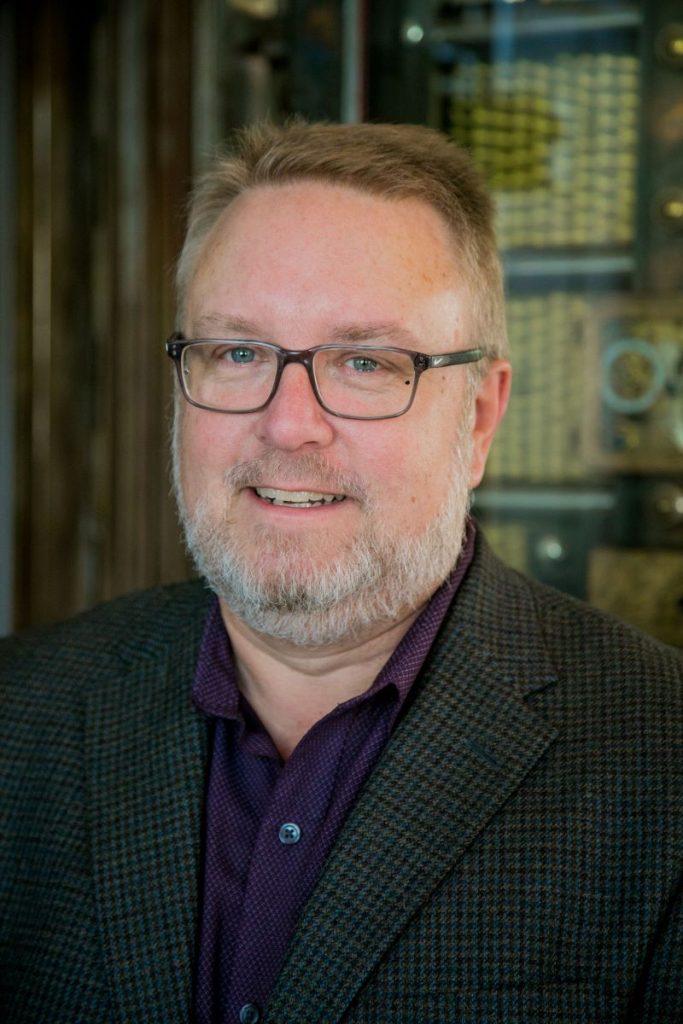
Steve Gantner, RA, CSI, CCS, CCCA, SCIP, AGCMO, is executive vice president and senior specification writer for Conspectus, Inc., a national specifications consultancy. Based in St. Louis, he has over 25 years of experience in various facility types and construction phases. His specialties include design-build, construction management, integrated project delivery, Owner project requirements documentation, procurement and construction specifications, quality assurance reviews and Conspectus Cloud expertise. Steve is passionate about education and collaboration between specifiers and construction teams and is available for classes and presentations.
