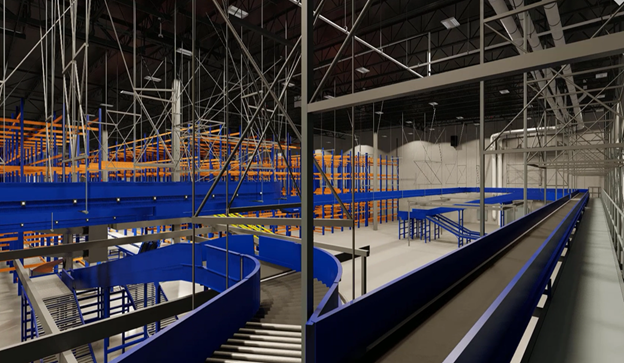
Since the introduction of Building Information Modeling (BIM), clash detection has been viewed by many in the AEC industry as the lowest of low-hanging fruit. If designers are already modeling in 3D, identifying spatial conflicts early to avoid coordination issues and on-site clashes seems straightforward. However, achieving effective results relies heavily on human factors and teamwork, particularly in choosing between “lonely BIM” and a collaborative BIM approach. High-performing coordination teams are especially seeing substantial benefits from this collaborative process.
For more than a decade now, even the most skeptical project stakeholders have acknowledged the value of clash detection paired with BIM coordination meetings led by VDC professionals or skilled model managers. This VDC-driven process will promote –– and if necessary, even force –– collaboration among key stakeholders, enabling early identification of significant issues in both the design and construction phases. This leads to reduced risk, improved quality and minimal rework, which in turn improves safety through fewer field manhours invested in that rework and the enablement of pre-fabrication and digital layout, all of which streamline project timelines. Sounds like utopia, right?
Yet, despite all these universally perceived benefits, why are some project teams still so caught up on the cost of implementation and the belief that not enough budget is available to support the effort? To combat this attitude, the Haskell team was interested in better defining exactly how much savings teams can expect to be attributed to clash detection and the overall BIM coordination process: 2x, 3x, 4x, 5x? And who pockets the savings?
To answer this, the Haskell team undertook an extensive ROI analysis on a $230 million design-build food project in California. The VDC team utilized Autodesk BIM 360 and Procore for model sharing, documenting all design and construction issues using the Newforma Konekt issue management platform (formerly BIM Track).
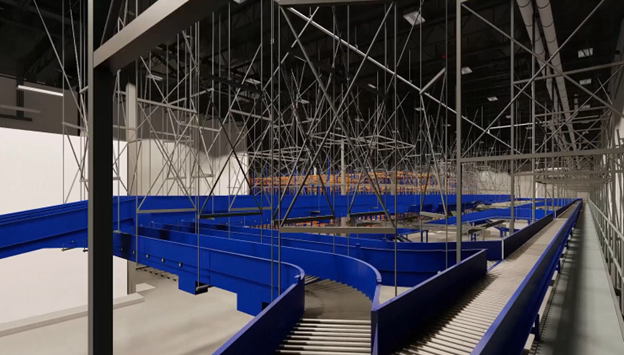
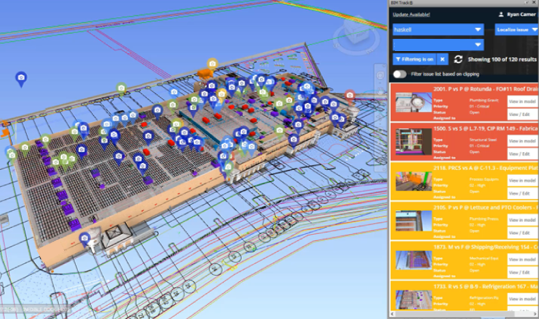
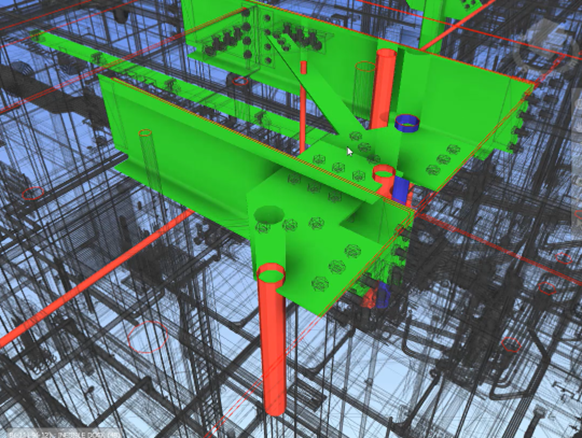
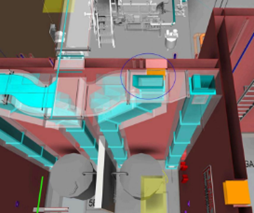
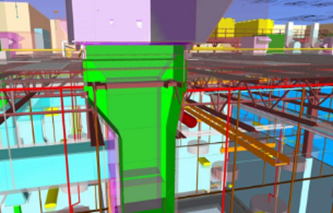
Clash Detection in Action
Each issue was categorized by phase (design or construction), assigned a priority (Critical, High, Medium, Low, Field Coordinate), work zone, and allocated to a responsible trade subcontractor or escalated to design discipline. The project management (PM) team responsible for ROI assessment then filtered the approximately 932 of 2000 total clashes, to review and assign cost magnitude to only the higher-priority items (Critical, High, and Medium). PMs grouped common clashes by scope and applied typical estimated cost values to those common occurrences, creating a consolidated basis of cost report.
Those items were then aggregated together into the table below:
Scope | Issues | Total Cost Avoided |
Conveyor Equipment | 42 | $ 283,500 |
Electrical Lighting | 61 | $ 51,850 |
Electrical Power | 92 | $ 269,100 |
Fire Protection Piping | 2 | $ 4,000 |
Fire Protection Sprinklers | 15 | $ 7,500 |
IMP Hangers | 11 | $ 17,600 |
IMP T-Bar | 18 | $ 76,500 |
Low Voltage Cable Tray | 22 | $ 80,850 |
Low Voltage Conduits | 13 | $ 38,025 |
Mechanical Duct | 129 | $ 145,125 |
Mechanical Equipment | 41 | $ 26,650 |
Mechanical Piping | 1 | $ 785 |
Plumbing Equipment | 12 | $ 5,580 |
Plumbing Gravity Piping | 200 | $ 70,000 |
Plumbing Pressure Piping | 181 | $ 171,950 |
Process Equipment | 2 | $ 20,000 |
Process Pipe | 6 | $ 15,000 |
Refrigeration Duct | 9 | $ 135,000 |
Refrigeration Equipment | 5 | $ 62,500 |
Refrigeration Piping | 19 | $ 95,000 |
Storage Racking | 18 | $ 213,750 |
Structural Steel | 33 | $ 420,750 |
TOTAL | 932 | $ 2,211,015 |
The results were staggering. For a $200,000 VDC labor effort, the project achieved $2.22 million in rework savings and an additional, conservative estimate of $542,000 in schedule savings from a one-month reduction in general conditions (GC) costs. The net savings was $2.55 million, or an ROI on the labor investment of 10x. Time to celebrate!
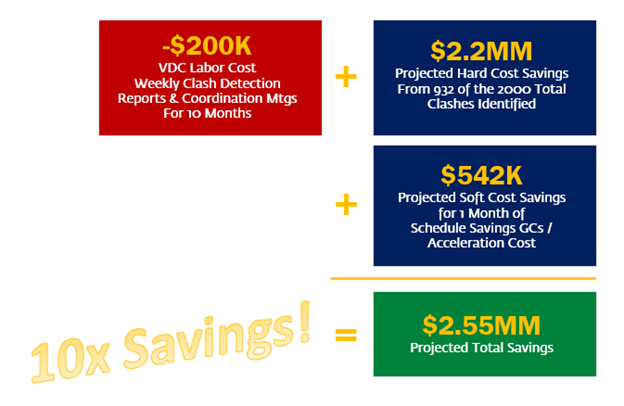
Planning for Success with Design-Build
Of course, achieving this level of success required thorough planning. BIM requirements were integrated early in the BIM Design Professional Services Agreement (PSA) for each design consultant (Fire Protection, Refrigeration, Telecommunications, and Packaging), while critical subcontractors were pre-qualified based on their BIM capabilities via Vendor Qualification Forms (VQF). Each subcontract included a BIM Attachment that outlined modeling, coordination, field execution tolerances, and handover responsibilities.
The design-build delivery method was also essential, allowing teams to collaborate from the outset. This early collaboration helped teams proactively identify and mitigate risks, catching issues early — well before fabrication and installation — which maximized the impact of rework and schedule savings.
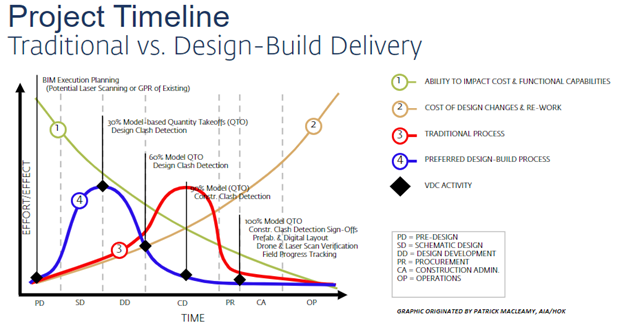
The Bottom Line
The ROI from clash detection on this project was eye-opening. Proactive BIM coordination not only prevented costly issues but delivered real savings — over $2.5 million in cost and time savings on this project alone. A $200k investment in BIM coordination translated into a 10x return. In today’s industry, VDC investments are not just smart — they’re essential for staying competitive.
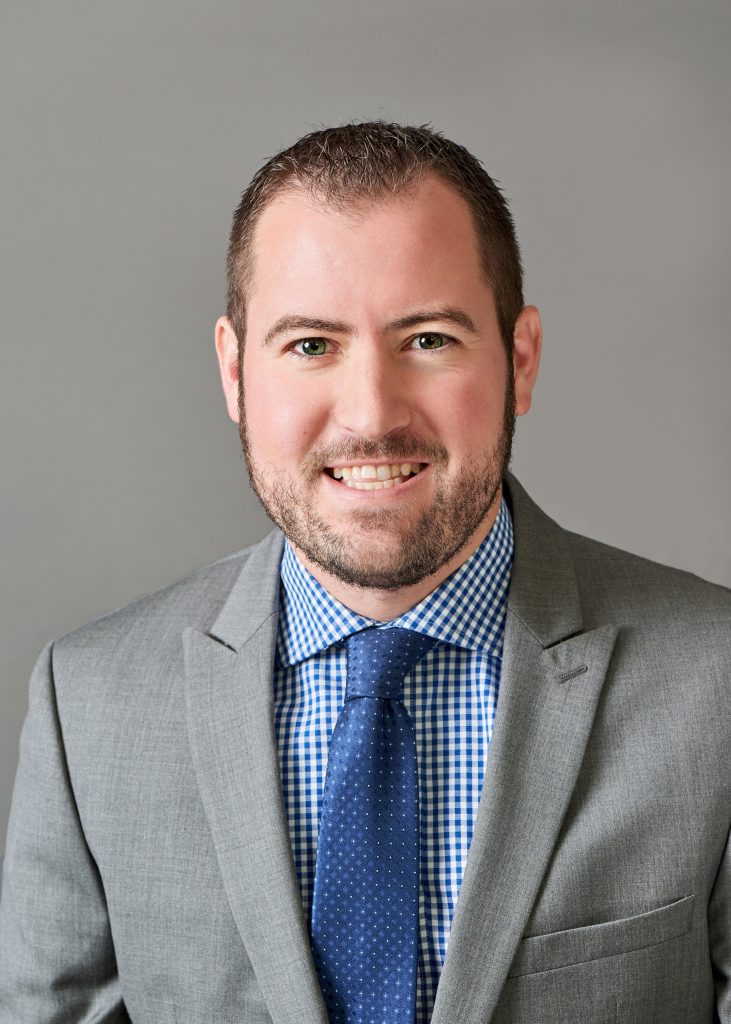
Ryan joined Haskell in 2007 and serves as Haskell’s Director of Virtual Construction (VDC/BIM). The VDC Group is dedicated to leveraging 3D Building Information Modeling (BIM) technology innovations throughout the organization and project lifecycle in design, preconstruction and field execution phases.
These VDC services, which reduce risk and increase efficiency, include model integration, coordination through automated clash detection, renderings, virtual reality walkthroughs, 4D construction schedule simulations, model-based quantity takeoff for estimating, robotic total station layout for self-perform concrete, 3D laser scan surveys, scan-to-BIM modeling, drone imagery and mapping.